Pharma Lab & Manufacturing
Broad range of services that combine IT, OT, and science expertise
Customised solutions incorporating a unique blend of IT, OT, and scientific expertise to support your pharmaceutical laboratory and manufacturing operations both day-to-day and as you modernise for the future.
Pharma Lab & Manufacturing Solutions
The type of support required by your pharmaceutical facility is changing. Those changing needs are being driven by the increasing use of technologies that automate and digitalise processes on the manufacturing floor and in the lab. This is in addition to more stringent quality controls and enhanced transparency requirements.
Managed services, professional services, and staffing solutions where science and technology come together will ensure your laboratory staff have the support, guidance, and expert help they need. Our solutions will help your pharma lab and production teams:
- Work more efficiently with improvements in productivity and resource utilisation.
- Modernise and optimise processes according to business needs.
- Drive continuous improvements in quality standards.
Unique Value Proposition
Westbourne offers a unique range of skills and capabilities to pharmaceutical operations. This includes technical expertise built up over several decades enabling us to provide a full array of technical solutions.
The real value of our solutions for pharmaceutical companies is our scientific and OT (operational technology) capabilities. Our team includes IT engineers, chemists, (QA) quality assurance specialists, validation engineers, and resources with a range of other skills crucial to your operations as a pharmaceutical manufacturing and/or pharma lab facility.
We also continuously upskill our team to enhance our capabilities. Get in touch with us today to arrange a consultation.
Pharma Lab Apprenticeship – Blueprint for the Industry
In addition to technical upskilling, we also have a unique Pharma Lab Apprenticeship initiative where we actively support our technical resources as they acquire the scientific skills that you need in your laboratory.
As a result, we can adapt our solutions to the specific technical and science requirements of your lab, the IT and OT requirements of your manufacturing processes, and the related QA, validation, and regulatory requirements that run across your organisation.
From helping you demonstrate GLP (Good Laboratory Practice) and GMP (Good Manufacturing Practice) to supporting technology upgrades and implementations to designing and managing laboratory system controls to digitalising systematic methods for your chemists to follow, we can help.
Get Technical / Scientific Support
Proactive Support
With our IT, lab technology, lab process, manufacturing, and compliance capabilities, we can help automate processes, enhance productivity, simplify operations, and improve accuracy. Our team will ensure the technology and equipment that your facility relies on is available and performing optimally, while proactively working with your team to improve performance, efficiency, safety, security, and compliance.
IT, Lab Technology, Lab Process, Manufacturing, and Compliance Expertise
We offer engineer-level IT, OT, and scientific expertise. This includes:
- FDA regulations including 21 CFR Part 11 covering electronic records and signatures. Our FDA regulatory expertise also includes GLP, GMP, and quality system requirements.
- EU MDR (medical device regulations), including Annex 11 covering computerised systems.
- Equipment validation – IQ (installation qualification), OQ (operational qualification), and PQ (performance qualification)
- CSV (computer system validation) and CSA (computer software assurance)
- Service delivery in compliance with ISO 9001 and ISO 13485
- GAMP5 qualified engineers
Pharma Lab Application Expertise
We also offer expertise in all common applications and systems used in pharmaceutical laboratories. Our system-agnostic approach means we support all application vendors, and our solutions include installation projects, upgrades, configuration optimisation, training, system interface monitoring, and ongoing support.
Our pharmaceutical laboratory application expertise extends to:
- LIMS (Laboratory Information Management Systems)
- CDS (Chromatography Data Systems), including Empower CDS
- SDMS (Scientific Data Management Systems)
- LES (Laboratory Execution Systems)
- ELN (Electronic Lab Notebooks)
- Document Management Systems
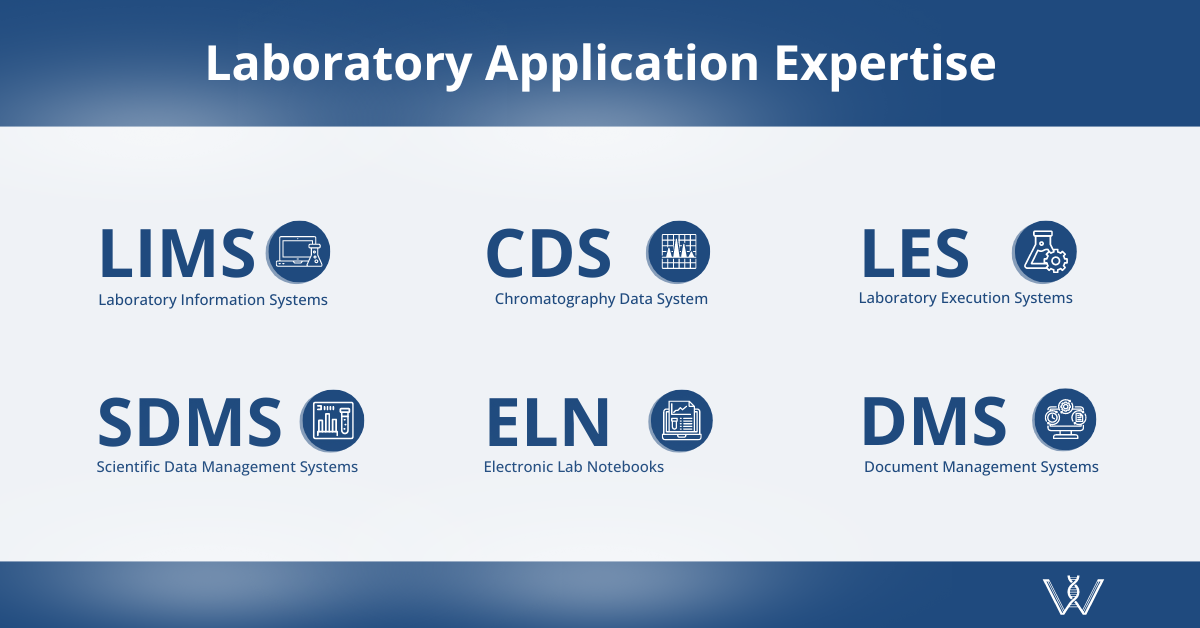
Managed Services Customised for Your Pharmaceutical Operations
Examples of the services and support we can provide through our Pharma Lab & Manufacturing solutions include:
Laboratory application support
IT support for PCs and related equipment in your production environment
IT and lab equipment monitoring and maintenance, freeing up your scientists and technicians to work on more value-adding tasks
Lab process automation and optimisation, including SOP (standard operating procedure) reviews, digitalising methods for your scientists and chemists to follow, and more
Quality process and quality management system (QMS) support, including CAPA (corrective and preventative action) support and batch record reviews
Validation and verification
Data management and optimisation, including data standardisation, integration, processing, storing, and reporting
Auditing of quality documents, procedures, and processes for efficiency, effectiveness, and compliance. Also, the creation and updating of validation master plans and validation templates
Lab instrumentation validation, calibration, and administration
IT infrastructure auditing and validation as well as IT infrastructure strategy development and implementation
Vendor and application stack assessments in addition to software licence optimisation
Risk assessments
Testing support including chromatography systems, test method validations, and performance analysis
Laboratory system controls as well as system and data backup and disaster recovery
Support ticketing
Reporting and data dashboards
The specific solution we provide to your pharma laboratory and manufacturing operations will be tailored to your exact requirements. It will also be scalable and flexible to meet the changing needs of your organisation as technologies advance, business priorities adapt, and regulatory requirements evolve.
What We Do
Our process typically starts with an assessment of your requirements, IT infrastructure, equipment, platforms, scientific methods, quality documentation, lab processes, lab controls, lab procedures, and more.
We’ll also conduct risk assessments before presenting you with a plan that delivers on your immediate requirements in addition to establishing your lab on a path of continuous operational and compliance improvement.
Pharma Lab & Manufacturing Consultation
Your laboratory and/or manufacturing environment, personnel, processes, and technologies are unique, as are your operational, quality, compliance, and business requirements. The first step in the process of getting the support your facility needs is to arrange a consultation with a member of the Westbourne team. Get in touch with us today.
Pharma Lab & Automation FAQs
What laboratory application vendors do you support?
At Westbourne, we take a vendor neutral approach to laboratory applications and platforms. This enables us to provide expert advice based on requirements rather than trying to push one application vendor over another. Our vendor-neutral approach also ensures our engineers are exposed to a wide range of systems. Combined with our experience in laboratory processes and workflows, we can provide the solutions and/or support you need, whatever your requirements.
Why should we automate or digitalise when our systems work well?
Manual systems, whether digital or paper-based, can and do work well in pharmaceutical laboratories. However, they are resource-intensive and time-consuming. There is also a high risk of human error, plus it is easy for data to be incomplete or become compromised or lost. Modernising your systems and processes will improve data accuracy, completeness, and availability, while also reducing compliance risks and enabling you to reallocate your resources to more value-adding tasks.
How do you ensure new technologies and processes are implement effectively?
There are a number of elements that ensure the successful implementation of optimised processes and new technologies. This includes getting a full understanding of your current processes and technologies. One of the most important elements, however, is engaging with laboratory staff throughout the entire process.
Pharmaceutical Digital Transformation
Learn More >
Pharma Lab and Manufacturing
Learn More >
On-Site ICT
Learn More >
Validation
Learn More >
Global Service Desk
Learn More >
Latest Insights
Maximising Pharmaceutical Digital Transformation ROI
Digital transformation is changing the way pharmaceutical companies run their businesses, manufacture products, and develop new therapies and treatments. These changes are positive, but it is essential that modernisation initiatives are justified by maximising ROI....
Understanding Process Validation in the Pharmaceutical Industry
Process validation is all about two essential requirements for manufacturing in the pharmaceutical industry:...
Digital Transformation Cybersecurity Considerations in the Pharmaceutical Industry
Companies in the pharmaceutical industry cannot stand still, so modernising through digital transformation is...
IT Support On-Site – How to Choose the Right Solution for Your Business
Most businesses require some level of IT support, from full support to augmenting in-house technical teams. While...
The Convergence of Science and Technology Expertise in the Pharmaceutical Industry
Pharmaceutical laboratory and manufacturing operations are changing. The implementation of business process automation...