Pharmaceutical Digital Transformation
Delivering real-world digital transformation results in highly regulated environments
Digital transformation is essential for pharmaceutical laboratory and manufacturing operations. We can help you decide on your strategy and approach for digital transformation initiatives from the first step to transformation at scale.
Collaborative Digital Transformation Success
Technologies, processes, and best practices that fall under the digital transformation umbrella can enhance your operations today and ensure you are prepared for the challenges and opportunities of the future. Working with the right partner is crucial to digital transformation success.
Our approach to strategy development and implementation starts with people. While digital transformation is about technology, your people are the main drivers of success. As a result, we’ll engage stakeholders at all levels of the organiation to build a culture of inclusion.
By embracing an inclusive approach to modernization project delivery, we can leverage the expertise of your team to drive innovation and achieve tangible, long-lasting results.
Digital Transformation with a Focus on People
- Identifying and engaging key stakeholders.
- Fostering open discussions, especially with technicians and operators as they have the highest level of knowledge of workflows, processes, challenges, and limitations.
- Engage in active listening and authentic consideration of suggestions and concerns
- Ensuring decision-making is collaborative within a structured process that ensures positive project progress.
- Establishing a continuous feedback loop.
Achieve Your Objectives
- Enhance process efficiency – digitalize manual processes, increase levels of automation, reduce the number of process steps, minimize operator involvement, and enhance process robustness in your lab and on your production lines to prevent errors and unplanned deviations.
- Make better use of data – integrate systems, including legacy systems, to eliminate data silos while maintaining the highest standards of security. This will give you enhanced oversight and will enable data-driven decision-making.
- Improve product quality – the optimization of QA (quality assurance) processes will improve product quality by minimizing nonconformities and, where nonconformities occur, identifying them accurately and quickly.
- Optimize compliance – compliance processes will be both more efficient and comprehensive, from day-to-day compliance workflows to periodic regulatory audits and everything in between.
- Increase operational agility – improve the ability of your facility to respond to regulatory changes, customer expectations, market conditions, economic challenges, and geopolitical events.
- Improve competitiveness – ensure your operations continue to be profitable while meeting the needs of your customers.
- Improve productivity – reduce errors and improve workforce productivity and OEE (overall equipment effectiveness) through process improvements, predictive maintenance, real-time oversight, and data-driven decision-making.
- Reduce risks – mitigate and, where possible, eliminate risks including compliance, commercial, and reputational risks, as well as operational, quality, and supply chain management risks.
Arrange a Consultation
How We Can Support Your Digital Transformation Journey
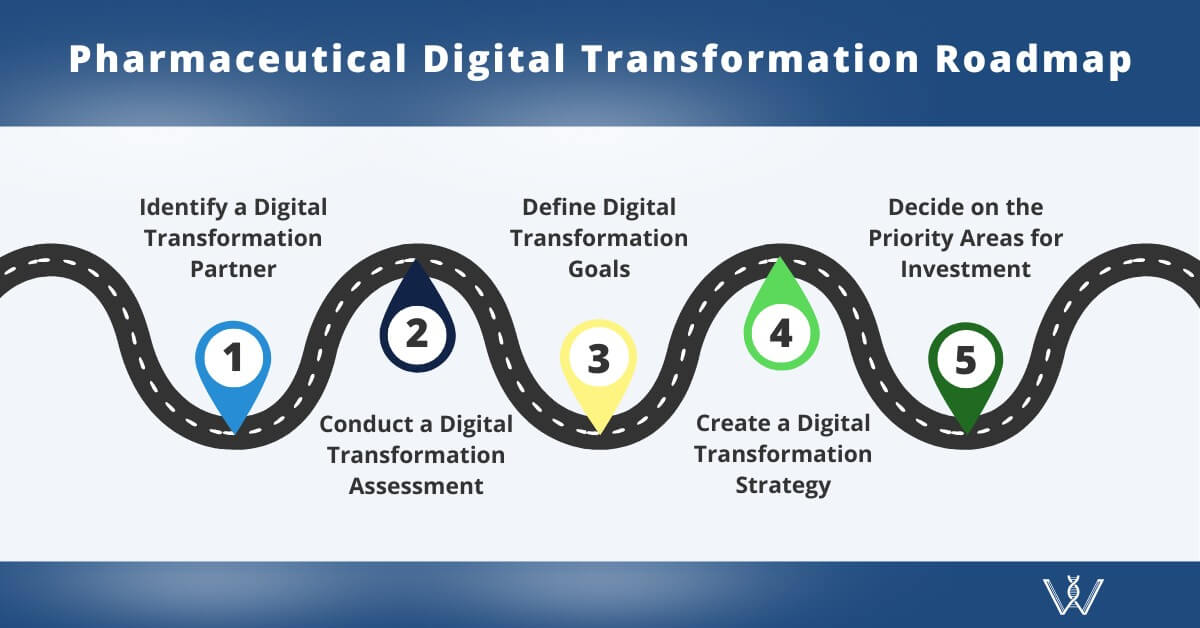
Strategy Development
We will use our expertise to assess your current infrastructure and processes, developing a technology roadmap and a plan to bridge the gap between IT and OT (operational technology). Systems integration, data standardization, and cybersecurity will all be key considerations in this process.
The strategy will be fully customized to your organization with a focus on minimizing risks and achieving maximum success within a realistic timeframe. We’ll also look ahead to ensure the projects delivered today establish the right foundation for further improvements in the future.
Project Management and Implementation
We’ll use our extensive expertise, proven processes, and experience working with pharmaceutical industry customers to ensure the successful implementation of new technologies and processes under the digital transformation umbrella.
This includes working closely with operators and technicians on your production lines and scientific resources in your laboratory to ensure project buy-in and to minimize the training curve. You will be kept informed every step of the way through an iterative approach to project delivery, with success measured against criteria set by you.
Pharmaceutical Digital Transformation Consultation
As specialists in digital transformation for the pharmaceutical industry, we are perfectly placed to help you move to the next stage of your digitalization journey. Get in touch with us today to arrange a consultation.
Pharmaceutical Digital Transformation FAQs
What is digital transformation in the pharmaceutical industry?
In the pharmaceutical industry, processes and workflows are often manual. Digital transformation involves using digital technologies to improve processes and workflows through automation, the integration of systems, and data. This applies not only at an operational level but also vertically through the IT systems of the business. It can also apply horizontally to supply chain partners.
Where do we start with pharmaceutical digital transformation?
Where to start is one of the most challenging elements for pharmaceutical companies looking at digital transformation. Our approach at Westbourne is to conduct an assessment that includes your IT infrastructure, operation technology environment, and current workflows and processes. We'll then provide advice and recommendations on the next stages of your digital transformation journey with objectives that include minimizing risks, establishing a foundation for future success, and delivering tangible results.
Are there compliance risks associated with digital transformation?
There are compliance risks with digital transformation just as there are compliance risks with any IT or infrastructure project in pharmaceutical organizations. However, not only can those risks be managed, you can also reduce overall compliance risks through digital transformation by modernizing processes, increasing automation, integrating systems, and utilizing new technologies.
Pharmaceutical Digital Transformation
Learn More >
Pharma Lab and Manufacturing
Learn More >
On-Site ICT
Learn More >
Validation
Learn More >
Global Service Desk
Learn More >
Latest Insights
Empower 3 Audit Trails and Logs Explained
In the context of the computerized systems used in GxP environments, audit trails are a chronological record that captures all actions and events related to data. As a result, audit trails are a key area of functionality in most laboratory applications, including...
A Complete Guide to Computer System Validation
Computer System Validation, or CSV, is a modern, risk-based methodology that confirms software used in pharmaceutical...
Why Multidisciplinary Skills Are Essential in Pharma Lab and Manufacturing Operations
Very specific skills are required to successfully, safely, and profitably run a pharmaceutical manufacturing and...
The GxP Implications of Windows 10 End-of-Life for Pharma Labs
Windows 10, the commonly used operating system in pharmaceutical laboratories, is reaching its end-of-life (EOL). The...
Technology-Focused Scientific Career Progression Pathways in the Pharmaceutical Industry
The pharmaceutical industry is changing with the introduction of advanced methodologies and the greater use of new...