Understanding Process Validation in the Pharmaceutical Industry
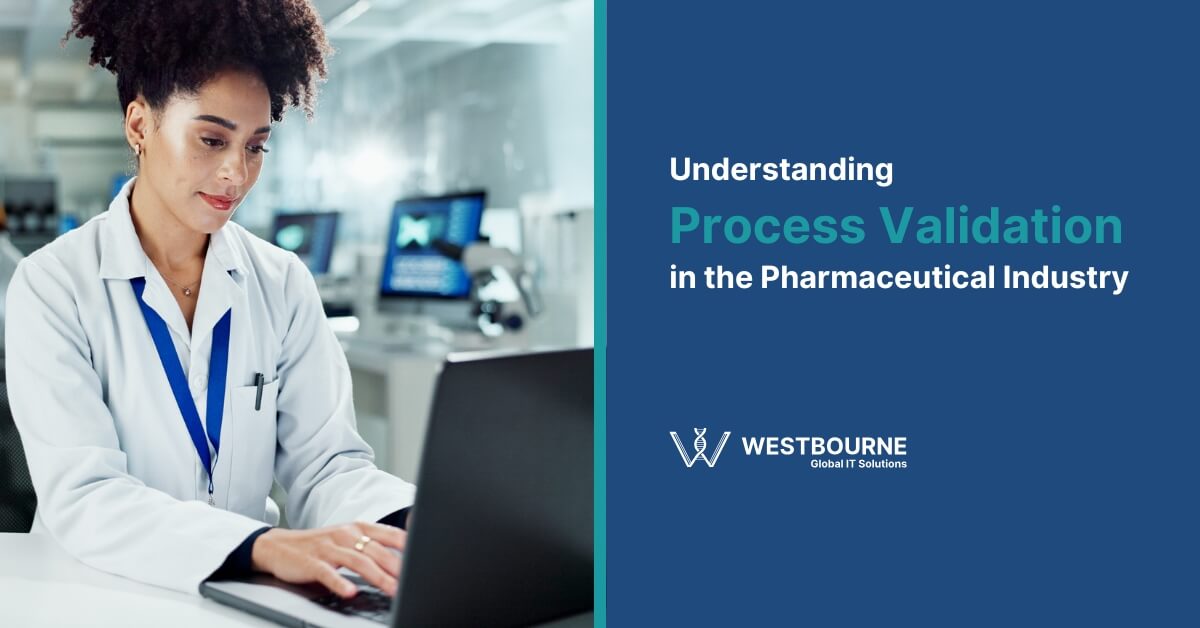
Process validation is all about two essential requirements for manufacturing in the pharmaceutical industry: consistency and reliability.
Deviations in the consistency or reliability of manufacturing processes result in sub-standard pharmaceutical products that can put patient safety at risk. Process validation helps manufacturers mitigate those risks by assessing and controlling the consistency and reliability of manufacturing processes.
Pharmaceutical manufacturing and laboratory operations are also often complex, enhancing even further the importance of methodically ensuring consistency and reliability.
Process validation is also essential for compliance, and it is a requirement of Good Manufacturing Practices (GMP). It requires data collection and analysis throughout all stages of production. There also needs to be documentation that demonstrates adherence to quality standards.
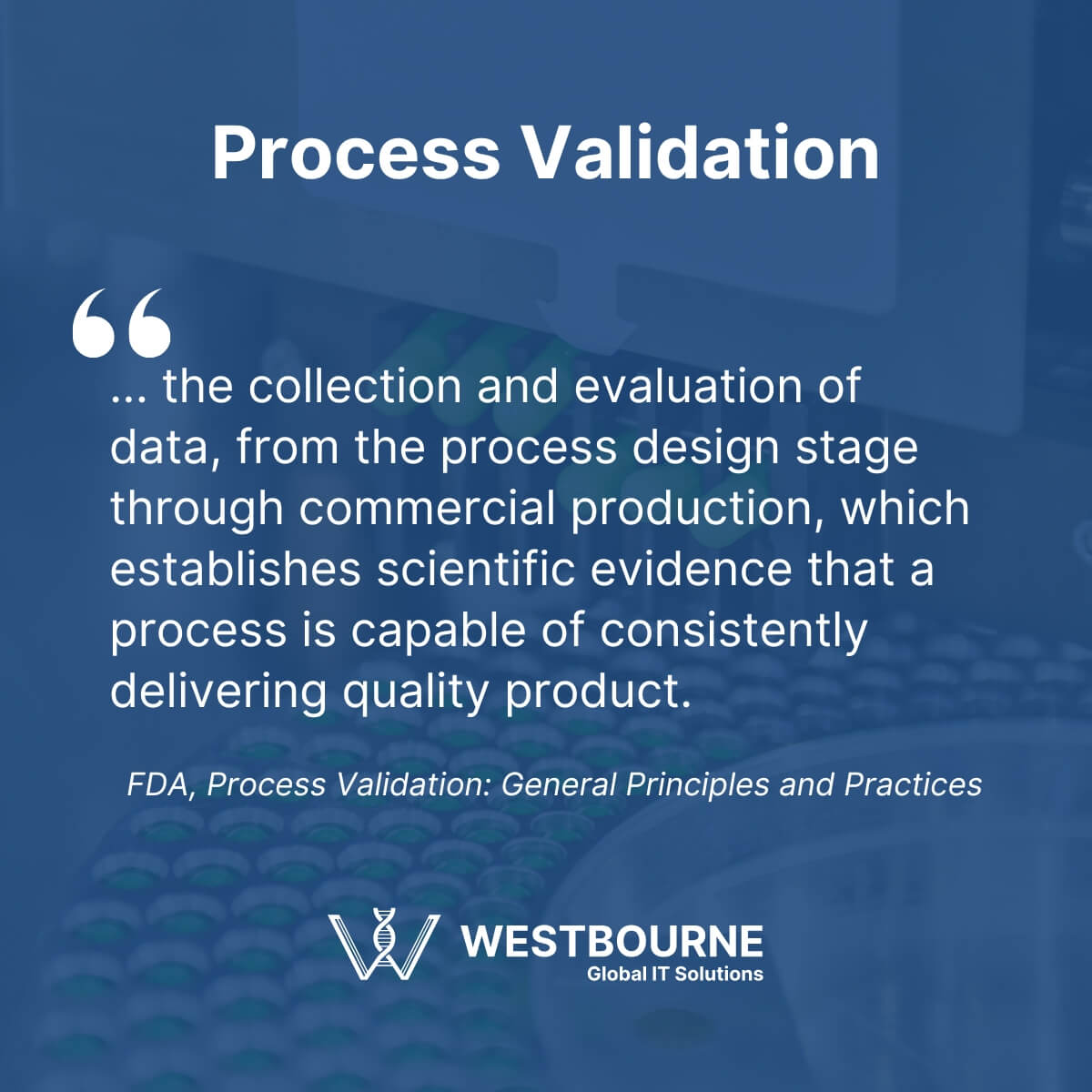
Core Principles of Process Validation
One of the core principles of process validation is the fact that testing a product after it has been manufactured with no other checks along the way is not enough to ensure consistent quality and patient safety. A lifecycle approach is, instead, required.
The objective is to produce Active Pharmaceutical Ingredients (APIs) and other drug products that can be consistently and reliably manufactured within defined parameters. The essential attributes of pharmaceutical products are the main areas of focus:
- Identity
- Strength
- Potency
- Purity
- Quality
Variations from defined parameters for any of these key attributes must be understood and controlled. This means:
- Identifying and understanding sources of variation, i.e., how and when a defined attribute of the product falls outside the required quality parameters.
- Assess the degree of variation outside the defined parameters.
- Analyze the likely impact of the variation.
- Control the variation using a risk-based approach, i.e., variations that represent the greatest risks should be subjected to higher levels of control.
Types of Process Validation
- Prospective – takes place during the development phase of a new drug.
- Concurrent – takes place during production using real-time data.
- Retrospective – uses historical data to evaluate and confirm process effectiveness.
- Revalidation – takes place in situations where a significant change has been made to a previously validated process. This could be altering a process in the laboratory or introducing new equipment.
Three Stages of Process Validation
The FDA (Food & Drug Administration in the US) has published guidance on Process Validation that aligns closely with GMP and regulations in other parts of the world. That guidance outlines three main stages of process validation.
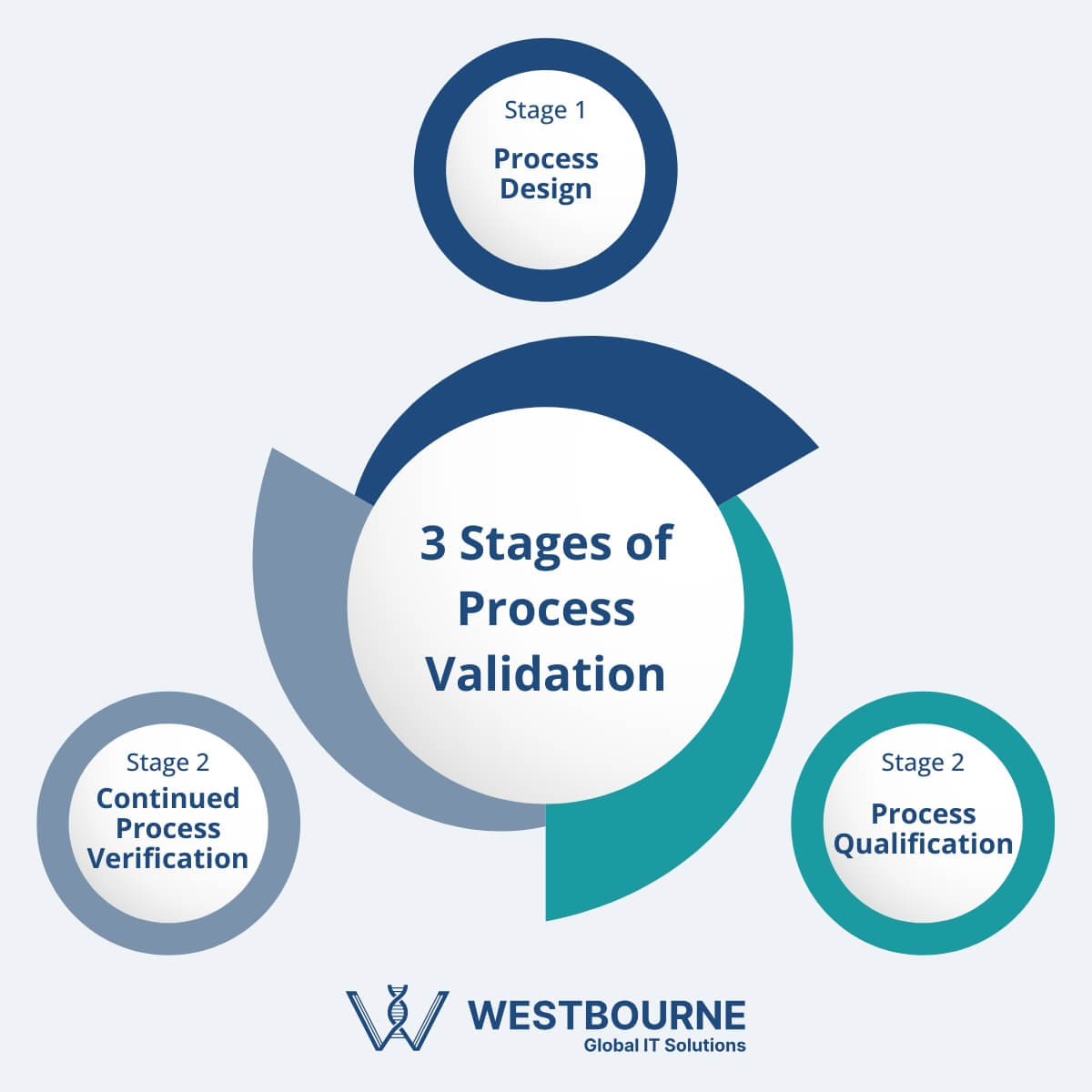
Stage 1: Process Design
Process Validation starts when designing the processes that will be used to manufacture the pharmaceutical product. Critical process parameters (CPPs) and critical quality attributes (CQAs) must be identified at this stage:
- CPPs – process variables that need to be monitored and controlled because of their potential to impact CQAs.
- CQAs – characteristics of a drug product that must be within a specified range, limit, or distribution. The characteristics could be chemical, physical, biological, or microbiological.
It is important to take a risk-based approach throughout all stages of Process Validation, including during the Process Design stage.
Stage 2: Process Qualification
Process Qualification is a specific regulatory requirement that must be completed before a pharmaceutical product can go into commercial production. It is where the process designed in the previous stage is evaluated for its reproducibility, i.e., can the production processes manufacture high-quality products within defined parameters, and can they do this consistently?
Process Qualification involves testing manufacturing processes under real-world conditions. This stage of Process Validation requires:
- Installation qualification (IQ) – to ensure production and related equipment have been installed properly and operate as intended.
- Operational qualification (OQ) – the testing of manufacturing processes under real-world operational conditions, i.e., on the factory floor rather than in the laboratory or in a computer simulation.
- Process performance qualification (PPQ) – to confirm the manufacturing processes deliver consistent quality standards when operating at full scale. According to FDA regulations, PPQ must be completed before a drug can be commercially distributed in the US. Similar rules apply in the EU and other jurisdictions.
Stage 3: Continued Process Verification
As Process Validation covers the full product lifecycle, it continues after the product has gone into commercial production. The objective is to ensure (and provide documented evidence) that manufacturing remains in a controlled state and continues to produce products to a consistent standard of quality.
Effective ongoing process validation enables the early identification and correction of quality deviations.
Common Challenges of Process Validation
- Accurately identifying CQAs and CPPs.
- Adapting to new technologies, automation solutions, or regulations
- Ensuring all stages of the process are properly documented with supporting scientific evidence.
These challenges (as well as situation-specific challenges) can be overcome with expert support from specialist providers.
Process Validation Best Practices
Team Approach
Regulators recommend that pharmaceutical organisations use a team approach to process validation. This includes involving expertise in:
- Process engineering
- Analytical chemistry
- Industrial pharmacy
- Microbiology
- Quality Assurance
- Manufacturing
- Operational Technology and IT
Digitalize Process Validation
Manual validation processes are resource-intensive, costly, and, often, unreliable. Adopting digital technologies and methodologies will reduce errors and costs by making process validation more efficient, accurate, and effective at ensuring products are manufactured to high standards.
Supporting Process Validation in Your Facility
At Westbourne, we have expert resources on our team covering a range of essential pharmaceutical disciplines across science, quality control, and technology. We can help with your process validation requirements – get in touch today to arrange a consultation.
Latest Insights
How On-Site IT Engineers Become Enablers in Your Organisation
There are many technical issues and tasks that can be supported by remote teams. Others, however, require the physical expertise of on-site IT engineers. On-site IT engineers shouldn't be viewed simply as resources performing specific functions. When set up properly,...
IT Support On-Site – How to Choose the Right Solution for Your Business
Most businesses require some level of IT support, from full support to augmenting in-house technical teams. While...
The Convergence of Science and Technology Expertise in the Pharmaceutical Industry
Pharmaceutical laboratory and manufacturing operations are changing. The implementation of business process automation...
Case Study: Empower CDS Validation and Wider Validation Improvements
Introduction Pharmaceutical laboratory operations are becoming increasingly reliant on technology as new platforms are...
A Year of Progress and Development at Westbourne
The world is changing fast, with new technologies and ways of working transforming all aspects of business. These...