Continuous Improvement of Empower CDS to Enhance Lab Operations
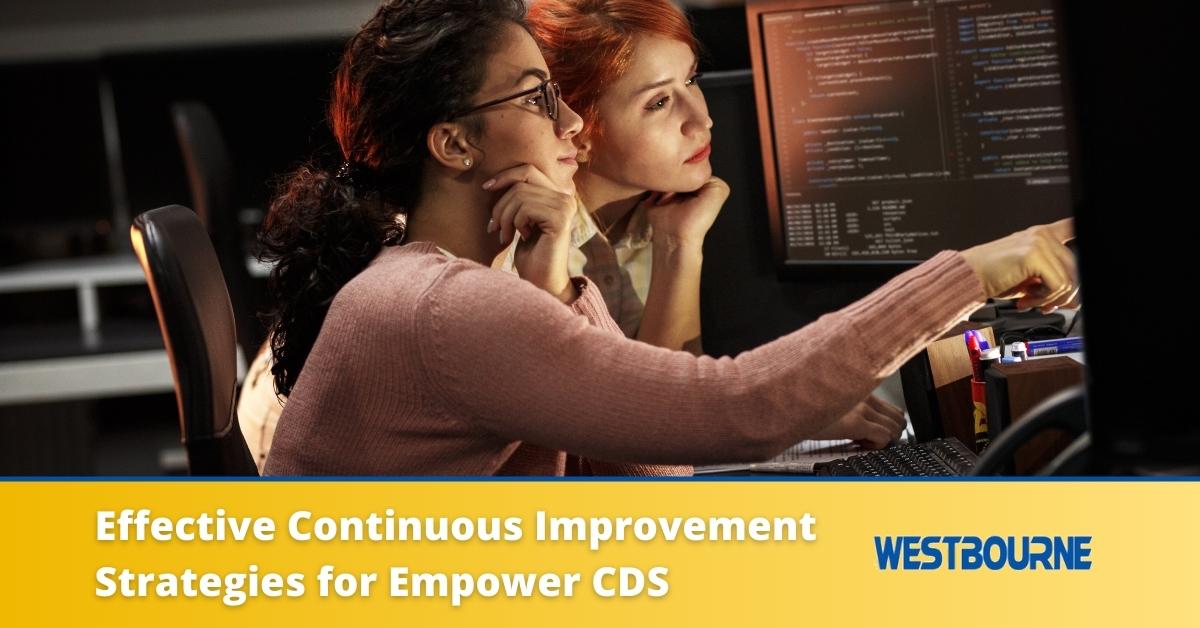
Empower CDS is an incredibly powerful tool that can deliver significant benefits for pharmaceutical and biopharmaceutical labs, big and small. It is also an incredibly complex tool, making continuous improvement of your Empower implementation a necessity.
There are two ways of successfully approaching continuous improvement of the Empower platform in your lab, and one that on the surface looks promising, but, in reality, is unworkable and ineffective.
So, in summary, here are the dos and don’ts of Empower continuous improvement:
- Don’t attempt to standardize your Empower CDS implementation across multiple labs
- Do implement global-level optimizations based on real-world data and experience
- Do implement site-specific optimizations based on your processes, products, and workflows
Let’s look at each in more detail with examples.
The Problem with Standardizing Empower Across Multiple Labs
No matter how much you attempt to standardize, no two installations or configurations of Empower are the same. Why? Every lab in the life sciences sector has its own processes, even within the same company.
Therefore, what works for one lab won’t work in another, resulting in one of two potential scenarios:
- The inefficiencies in Empower-driven processes and workflows can be addressed through optimization, causing divergence between Empower configurations and rendering your standardization efforts obsolete.
- The inefficiencies are not addressed, resulting in staff working with Empower processes that are not fit for purpose. In this scenario, it is impossible to get the full benefit of your Empower investment. There could also be knock-on impacts on the productivity of your quality function and, in manufacturing facilities, upstream impacts on the production line.
So, if standardization doesn’t work, how do you ensure Empower works for your lab today and into the future? The starting point is ongoing global-level optimizations.
Global Level Optimizations of Empower CDS
At Westbourne, we have insight into Empower CDS user and performance data from multiple labs. This allows us to identify errors where we can then develop solutions that can be implemented across all customer installations.
One recent experience is a perfect example. There was an update released for Empower that improved the platform and added new features, but the update also resulted in a problem with pushing and saving data on servers.
Our team identified this issue and started investigating. We discovered the cause of the problem was related to unstable network connections, enabling us to develop a solution. That solution changed the controls, whereby the system now waits for samples to be completed before data is sent to the server. This reduces the possibility of corruption while data is being transferred.
We were then able to roll out this solution to all customers with Empower implementations impacted by this data corruption problem.
Site-Specific Continuous Improvement of Empower CDS
While global-level optimizations of Empower CDS will benefit your lab, the biggest gains come from site-specific optimizations, i.e., optimizations based on your workflows and how you use the Empower platform.
However, one of the challenges with site-specific ongoing improvement of Empower CDS is identifying the optimization opportunities that exist. In most lab environments, technicians can use Empower and not know there is potentially a better way.
This is where data and Empower expertise are critical. In other words, you need engineers with in-depth knowledge of the Empower platform continuously assessing how you are actually using Empower to identify areas for improvement.
Practical Examples of Site-Specific Empower Improvements
We can again use our experience at Westbourne as examples of this optimization strategy in practice. Our team of Empower specialists constantly monitors the user experience of our customers with the objective of making the software easier to use and more aligned with an individual lab’s workflows and processes. The more process steps, obstacles, and errors that we can eliminate, the better.
We recently went through this process with a customer, where the company’s lab staff were changing the processing method a number of times to make it fit with requirements. Our team identified this re-processing inefficiency in the data, so set about developing a solution.
That solution was to define a standard processing method that eliminated the need for changing anything. When implemented, the company benefited from efficiency savings, reduced error rates, and the elimination of unnecessary double work.
Another example is where we customized the user controls in Empower to meet the requirements of one of our customers. The default user controls in Empower are designed to meet GMP (Good Manufacturing Practice) standards, so they are very restrictive.
Our customer didn’t need to comply with GMP, but they did need greater flexibility when it came to user controls. Our team made this possible by optimizing the lab’s Empower implementation according to its specific requirements.
Improvements Are Always Possible
The deeper you get into Empower CDS, the more you can see lab process improvement opportunities. It is critical that any improvements you make are based on your specific requirements.
However, you might not even know an optimization or improvement is possible. This is where expert Empower support becomes essential. Get in touch with us today to find out more.
Latest Insights
17 Features You Need in a Global Service Desk
In today's digitally connected world, a global service desk is more than just a support function. It’s the backbone of seamless operations, uninterrupted service, and exceptional user experiences. Choosing the right global service desk provider is a pivotal decision...
How On-Site IT Engineers Become Enablers in Your Organisation
There are many technical issues and tasks that can be supported by remote teams. Others, however, require the physical...
The GxP Implications of Windows 10 End-of-Life for Pharma Labs
Windows 10, the commonly used operating system in pharmaceutical laboratories, is reaching its end-of-life (EOL). The...
Maximizing Pharmaceutical Digital Transformation ROI
Digital transformation is changing the way pharmaceutical companies run their businesses, manufacture products, and...
Understanding Process Validation in the Pharmaceutical Industry
Process validation is all about two essential requirements for manufacturing in the pharmaceutical industry:...